极片制作一般工艺流程为:活性物质,粘结剂和导电剂等混合制备成浆料,然后涂敷在铜或铝集流体双面,经枯燥后去除溶剂构成极片,极片颗粒涂层经过压实细密化,再裁切或分条。辊压是极片最常用的压实工艺,相对于其他工艺进程,辊压对极片孔洞结构的改动巨大,并且也会影响导电剂的散布状况,然后影响电池的电化学功能。为了取得最优化的孔洞结构,充分认识和了解辊压压实工艺进程是十分重要的。
辊压工艺根本进程
工业生产上,池极片一般选用对辊机接连辊压压实,如图1所示,在此进程中,双面涂敷颗粒涂层的极片被送入两辊的空隙中,在轧辊线载荷效果下涂层被压实,从辊缝出来后,极片会产生弹性回弹导致厚度添加。因而,辊缝巨细和轧制载荷是两个重要的参数,一般地,辊缝要小于要求的极片终究厚度,或载荷效果能使涂层被压实。别的,辊压速度的巨细直接决议载荷效果在极片上的坚持时刻,也会影响极片的回弹,终究影响极片的涂层密度和孔隙率。
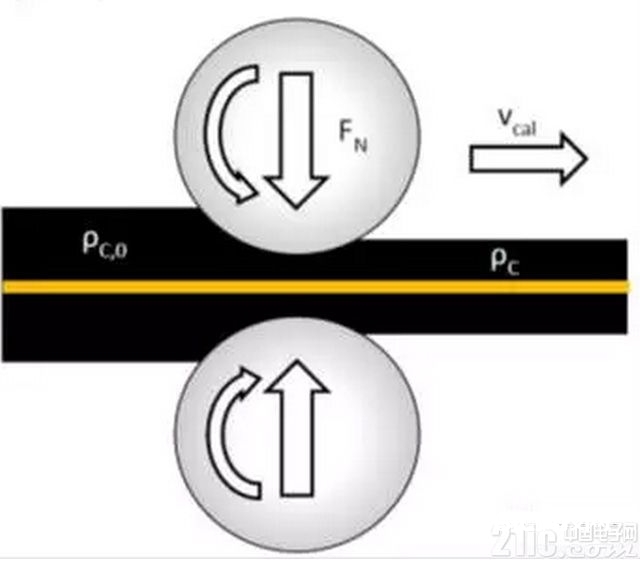
图1 极片辊压进程示意图
在轧制速度Vcal下,极片经过辊缝时,线载荷可由式(1)核算:
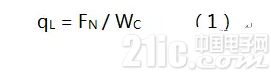
其间,qL为效果在极片上的线载荷,FN为效果在极片上的轧制力,Wc为极片涂层的宽度。
辊压进程极片微观结构的演化
经过辊缝,极片被压实,涂层密度由初始值ρc,0变为ρc。压实密度ρc可由式(2)核算:
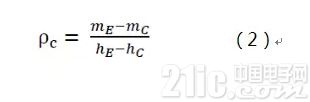
其间,mE为单位面积内的电极片分量,mC为单位面积内的集流体分量,hE为电极片厚度,hC为集流体厚度。而压实密度与极片孔隙率相关,物理上的涂层孔隙率εc,ph可由式(3)核算,其意义为颗粒内部的孔隙和颗粒之间的孔隙在涂层的体积分数:
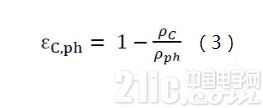
其间,ρph为涂层各组成资料均匀物理真密度。
在实践的辊压工艺中,跟着轧制压力改变,极片涂层压实密度具有必定规则,图2为极片涂层密度与轧制压力的联系。
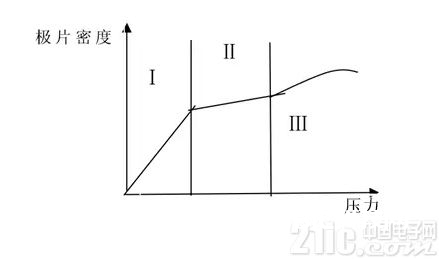
图2 极片涂层密度与轧制压力的联系
曲线 I 区域,为第一阶段。此阶段压力相对较小,涂层内颗粒产生位移,孔隙被填充,压力稍有添加时,极片的密度快速添加,极片的相对密度改变有规则。
曲线 II 区域,为第二阶段。此阶段压力持续添加,极片经紧缩后,密度已增高。孔隙已被填充,浆料颗粒产生了更大的压实阻力。压力再持续进步,但极片密度添加较少。因而时浆料颗粒间的位移现已削减,颗粒很多的变形还没开端。
曲线 III 区域,为第三阶段。当压力超越必定值后,压力添加极片密度也会持续添加,随后又逐步陡峭下来。这是因为当压力超越浆料颗粒的临界压力时,颗粒开端变形、破碎,颗粒内部的孔隙也被填充,使极片密度持续增大。但当压力持续添加,极片密度的改变逐步陡峭。
实践极片轧制进程的状况十分复杂。在第一阶段,粉末体的细密化尽管以浆料颗粒的位移为主,但一起也有少数的变形。在第三阶段,细密化以浆料颗粒的变形为主,一起也会存在少数位移。
别的,因为正负极资料自身性质差异,正负极极片辊压进程微观结构改变也不相同。正极颗粒资料硬度大,不简单产生变形,而石墨负极硬度小,压实进程会产生塑性变形,如图3所示。中等程度的压实会减轻石墨的塑性变形量,锂离子嵌入和脱出阻力更小,电池循环稳定性更好。而载荷过大或许导致颗粒破碎。正极极片中因为活性物质导电性很差,与负极比较,辊压进程引起导电剂散布改变对电子传导影响更显着。
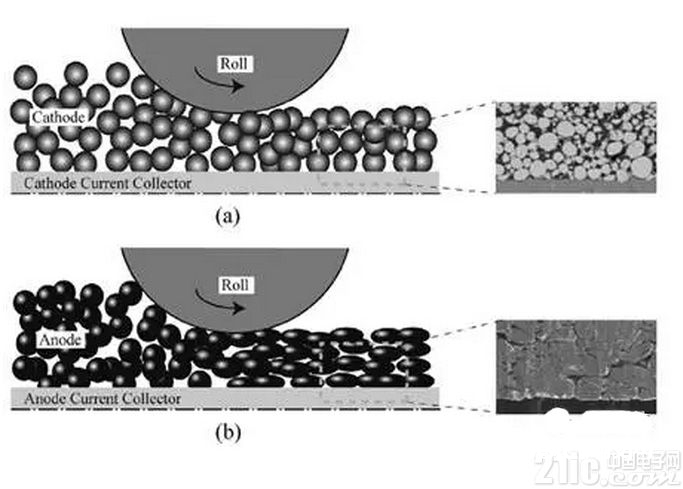
图3 正负极极片辊压颗粒位移和变形示意图
压实密度对电化学功能的影响
在电池极片中,电子传导首要经过,而锂离子传导首要经过多孔结构中的电解液相进行,电解液填充在多孔电极的孔隙中,锂离子在孔隙内经过电解液传导,锂离子的传导特性与孔隙率密切相关。孔隙率越大,相当于电解液相体积分数越高,锂离子有用电导率越大。而电子经过活物质或碳胶持平固相传导,固相的体积分数,迂曲度又直接决议电子有用电导率。孔隙率和固相的体积分数是彼此对立的,孔隙率大必定导致固相体积分数下降,因而,锂离子和电子的有用传导特性也是彼此对立的。
一方面,压实极片改进电极中颗粒在之间的触摸,以及电极涂层和集流体之间的触摸面积,下降不可逆容量丢失触摸内阻和沟通阻抗。另一方面,压实太高,孔隙率丢失,孔隙的迂曲度添加,颗粒产生取向,或活物质颗粒外表粘合剂被揉捏,约束锂盐的分散和离嵌入/脱嵌,锂离子分散阻力添加,电池倍率功能下降。
辊压工艺参数的影响规则
前面说到辊压工艺直接决议极片的多孔结构,而线载荷、速度等辊压工艺参数对极片微观结构到底有什么样的影响呢?德国布伦瑞克工业大学研讨人员Chris Meyer等做了相关的研讨。
他们研讨发现,锂离子电池极片的压实进程也遵从粉末冶金范畴的指数公式(4),这提醒了涂层密度或孔隙率与压实载荷之间的联系。
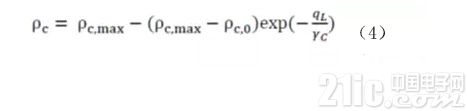
其间,和能够经过试验数据拟合得到,别离标明某工艺条件下涂层能够到达的最大压实密度以及涂层压实阻抗。
表1 试验用正负极极片参数

研讨者对表1中所示NCM三元正极极片和石墨负极极片进行辊压试验,研讨辊压工艺参数对极片涂层密度和孔隙率的影响规则。依据资料物理真密度核算,当孔隙率为0%时,正极涂层密度应该为4.3 g/cc,负极涂层密度应该为2.2 g/cc。而实践上依据试验数据拟合得到了参数(见表2)标明正极涂层到达的最大密度约3.2 g/cc,负极约为1.7 g/cc。
图4是辊压线载荷和正负极极片涂层密度的联系,不同的载荷和辊压线速度条件下收集试验数据点,然后选用指数方程(4)对数据进行拟合,得到相应的方程拟合参数,列入表2中。标明为涂层的压实阻抗,较低值标明跟着线载荷添加,涂层密度能够较快到达最大值,而较高的阻抗值标明涂层密度较慢到达最大值。从图4和表2中可见,辊压速度对涂层密度影响较小,较小的速度导致涂层密度稍微添加。别的,正负极极片的压实进程差异大,正极极片压实阻抗大约为负极的一倍多,这是因为正负极资料特性差异引起的,正极颗粒硬度大,压实阻抗大,而负极颗粒硬度小,压实阻抗小,更简单辊压压实。
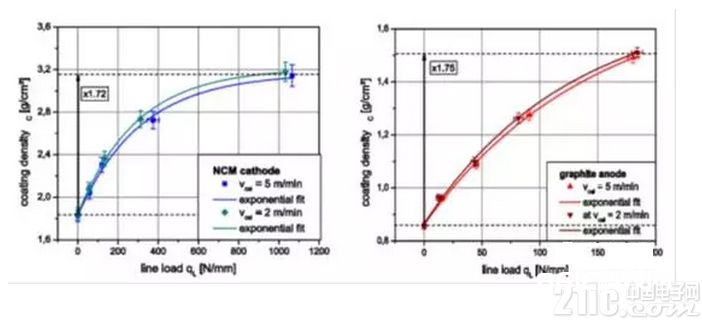
图4 线载荷与正负极极片涂层压实密度的联系
表2 不同辊压工艺条件下拟合得到的参数值
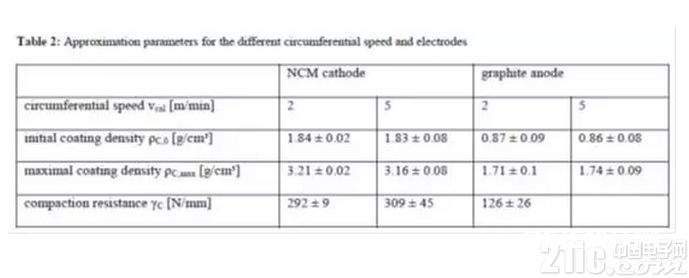
此外,从孔隙结构视点剖析辊压工艺的影响。电池极片涂层的孔隙首要包括两类:颗粒资料内部的孔隙,尺度为纳米-亚微米级;颗粒之间的孔隙,尺度为微米级。图5是不同辊压条件下正负极极片中孔径散布状况,首要很显着能够看到极片压实能够减小孔径尺度并下降孔隙含量。跟着压实密度添加,与正极比较,负极孔径尺度更显着下降,这是因为负极涂层压实阻抗低更简单被辊压压实。一起数据标明辊压速度对孔隙结构的较小。
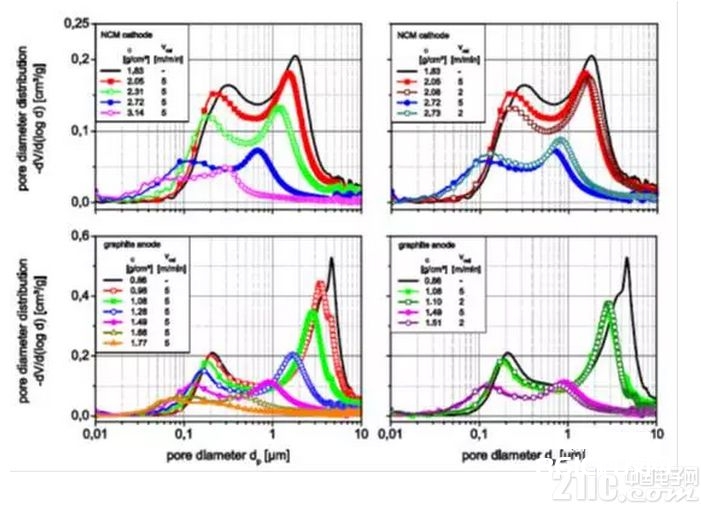
图5 不同辊压条件下孔径散布
从涂层的孔隙率视点考虑,辊压线载荷与涂层孔隙率之间也能够经过指数方程拟合得到规则,图6是线载荷与正负极极片涂层孔隙率的联系,不同的线载荷效果下对正负极极片进行辊压,经过物理真密度核算孔隙率、一起也经过试验丈量涂层的孔隙率,得到的数据点作图并进行线性拟合,成果如图6所示。
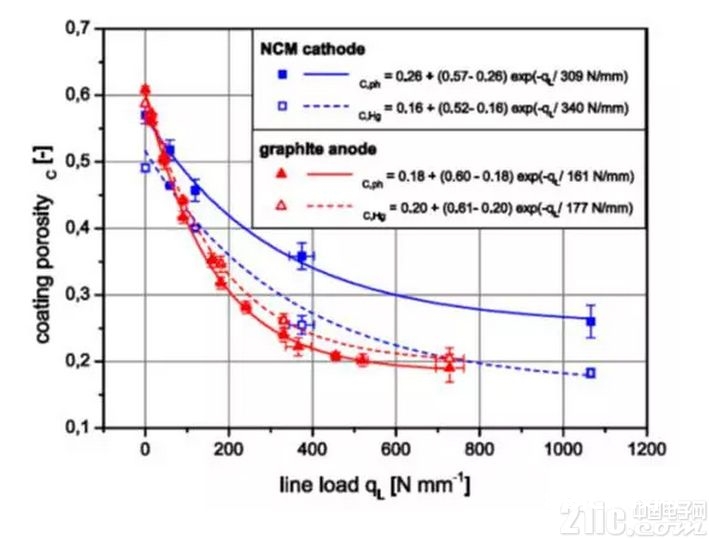
图6 线载荷与正负极极片涂层孔隙率的联系
辊压工艺对锂电池极片微观结构影响巨大,特别是对多孔结构,因而,辊压工艺激烈影响电池功能。总归,在锂电池技术研讨与开发中,咱们相同需求特别重视制作工